The aim of the article is to provide a comprehensive overview of ABC analysis in inventory management. We’ll go over the basic ideas and values of ABC analysis, as well as all of its advantages and practical steps for implementation. Real-world case studies will be used to show the actual benefits that can be obtained by implementing ABC analysis into inventory management techniques.
By the end of this article, you will have a solid understanding of how ABC analysis can improve inventory management, optimize resources, and ultimately contribute to the success of business operations. Whether new to inventory management or looking to improve your current methods, this article will provide the knowledge you need to enhance efficiency and profitability.
Inventory Management Meaning
Inventory management is the lifeblood of any successful company. It’s the delicate balance of maintaining just enough inventory on hand to meet customer demand while avoiding the risks of overstocking and locking up too much capital. Businesses of all sizes and industries realize that efficient inventory management may have a significant impact on profitability, cash flow, and customer satisfaction. Read more about inventory management.
when it comes to ABC Analysis, is a concept that has become an important component in inventory management. At its core, it is a mechanism for categorizing inventory goods based on their importance and value to the company. The concept is simple but powerful: not all inventory items are created equal. Some goods are more important than others, and ABC analysis assists firms in identifying and focusing their resources on managing the most critical items more successfully. The ABC analysis principles are generally relevant whether you run a retail store, a manufacturing plant, or an e-commerce organization.
Understanding ABC Analysis
ABC analysis, also known as ABC classification, is a fundamental inventory management technique used to identify inventory items based on their relevance and value to the company. This method divides inventory items into three groups: A, B, and C, with each group reflecting a distinct level of importance.
The history of ABC analysis can be traced back to the beginning of the 20th century, when it was popularized by Vilfredo Pareto, an Italian economist who recognized the 80/20 principle, also known as the principle of Pareto. This idea proposed that a relatively small fraction of products, frequently 20%, are responsible for the majority of the impacts, in this example, the majority of inventory value or utilization. Businesses and supply chain professionals recognized the importance of this idea throughout time and developed the ABC analysis as a systematic technique for managing their inventory more efficiently.
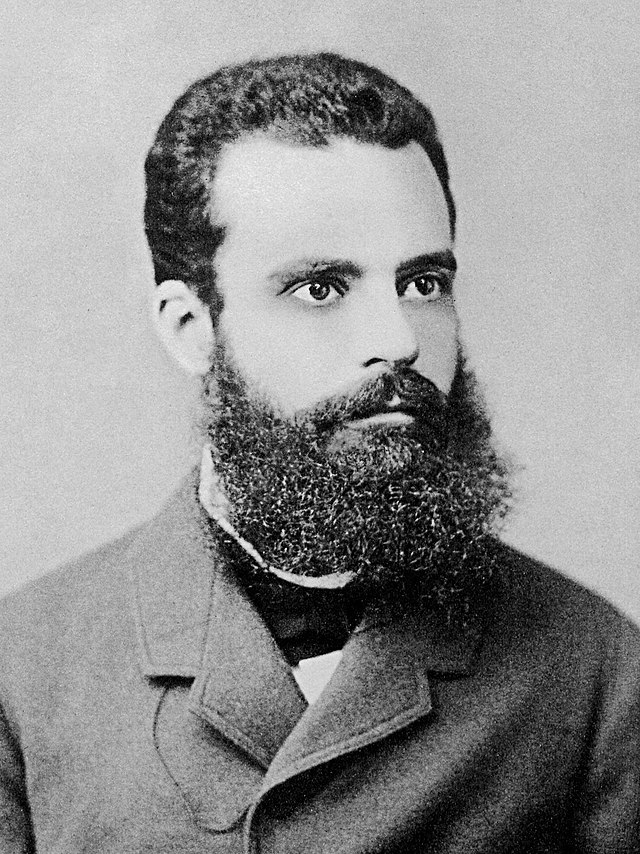
The key ideas of ABC analysis are pretty simple. Inventory items are classified according to particular requirements, which are usually connected to their worth, usage frequency, or importance. The main objective is to find and differentiate between items with a significant influence on the business and those with little impact.
The ABC classification is typically defined as follows:
A-class items are high-value, high-impact products that account for just a small portion of total inventory items but account for an important percentage of inventory value. These concerns are closely monitored and given special attention.
B-class items are mid-value items that are somewhat important, falling in the middle of the scale. They account for a moderate share of inventory items and value.
C-class items are low-value, low-impact items that make up a considerable component of the inventory but account for a lower portion of the inventory value. They are normally managed with less care.
ABC Analysis Example
Consider a real-life example to better understand the ABC classification process. Consider a retail store that sells a variety of things. In this case:
High-end electronic devices or designer clothing are examples of A-class items. These are high-priced items that have a major impact on the store’s revenue.
B-class items could include everyday products such as home appliances or normal apparel. They are reasonably priced and add to overall sales.
C-class items are likely to be low-cost, high-turnover goods, such as basic office supplies. While they are required for operations, they have little impact on revenue or profit margins.
Advantages of ABC Analysis
1. Cost Saving
One of the most notable advantages of applying ABC analysis in inventory management is the possibility of significant cost savings. Businesses can better manage their resources by categorizing inventory items into A, B, and C classes. A-class items, which represent the most valuable and significant components, receive special attention, ensuring that the company maintains the best stock levels. This strategic focus helps to limit the risk of stockouts, which can result in lost revenue and unsatisfied consumers. At the same time, it reduces the retention of surplus inventory, which can tie up a large amount of money. Businesses can take a more relaxed and cost-effective approach with B and C-class items because they are not as vital to operations.
2. Improved decision-making and forecasting
ABC analysis gives businesses a better grasp of the relative importance of each item in their inventory. This deeper understanding leads to better decision-making and forecasting. Businesses can create better demand estimates and handle resources more effectively.
3. Reduction in stockouts and excess inventory
ABC analysis enables careful management of A-class items, resulting in a large reduction in stockouts, a situation in which products are not accessible when customers wish to buy them. This is especially important for businesses that strive to meet client demands on a constant basis. At the same time, reducing inventory levels for C-class items reduces the possibility of excess stock. This saves capital from being tied up in items of secondary importance, which can have a negative influence on a company’s bottom line.
4. Enhanced supplier relationships and negotiations
Another significant advantage of ABC analysis is its ability to improve supplier relationships and negotiations. Businesses can engage with their suppliers strategically by categorizing products by priority. Companies can form more robust relationships and negotiate favorable conditions to ensure a constant supply of A-class items, where the stakes are higher. For B and C-class items, on the other hand, businesses can take a more cost-effective strategy, utilizing economies of scale and exploring cost-cutting strategies in their relations with suppliers.
Limitations of ABC Analysis
1. Subjectivity in Categorization
The categorization criteria used can be fairly subjective. Individuals or groups may prioritize criteria differently, resulting in disparate outcomes.
2. Static Analysis
ABC analysis is relatively static because it is based on past data. It may be less effective in highly dynamic industries since it does not account for quick market changes or unexpected fluctuations in demand.
3. Neglect of Lower Classes
The focus placed on A-class products may lead to the neglect of B and C-class items, reducing operational flexibility and overlooking significant cost-saving options.
4. Cost of Implementation
The initial implementation of ABC analysis could take time, resources, and technological investment, which might be prohibitively expensive for small businesses.
5. Overhead
Excessive focus on A-class products may result in increased operational costs due to strict monitoring and management.
Conclusion
In conclusion, ABC analysis is an important method in inventory management, providing firms with an organized strategy to categorize products depending on their importance. This categorization into A, B, and C classes allows for more efficient resource allocation, which leads to cost savings, better decision-making, and stronger supplier relationships. We suggest companies of all sizes use ABC analysis as a core tool for enhancing inventory management. This method, whether for a small retail operation or a huge manufacturing plant, provides a road to increased profitability and operational efficiency.